Understanding Custom CNC Machining: A Gateway to Precision Manufacturing
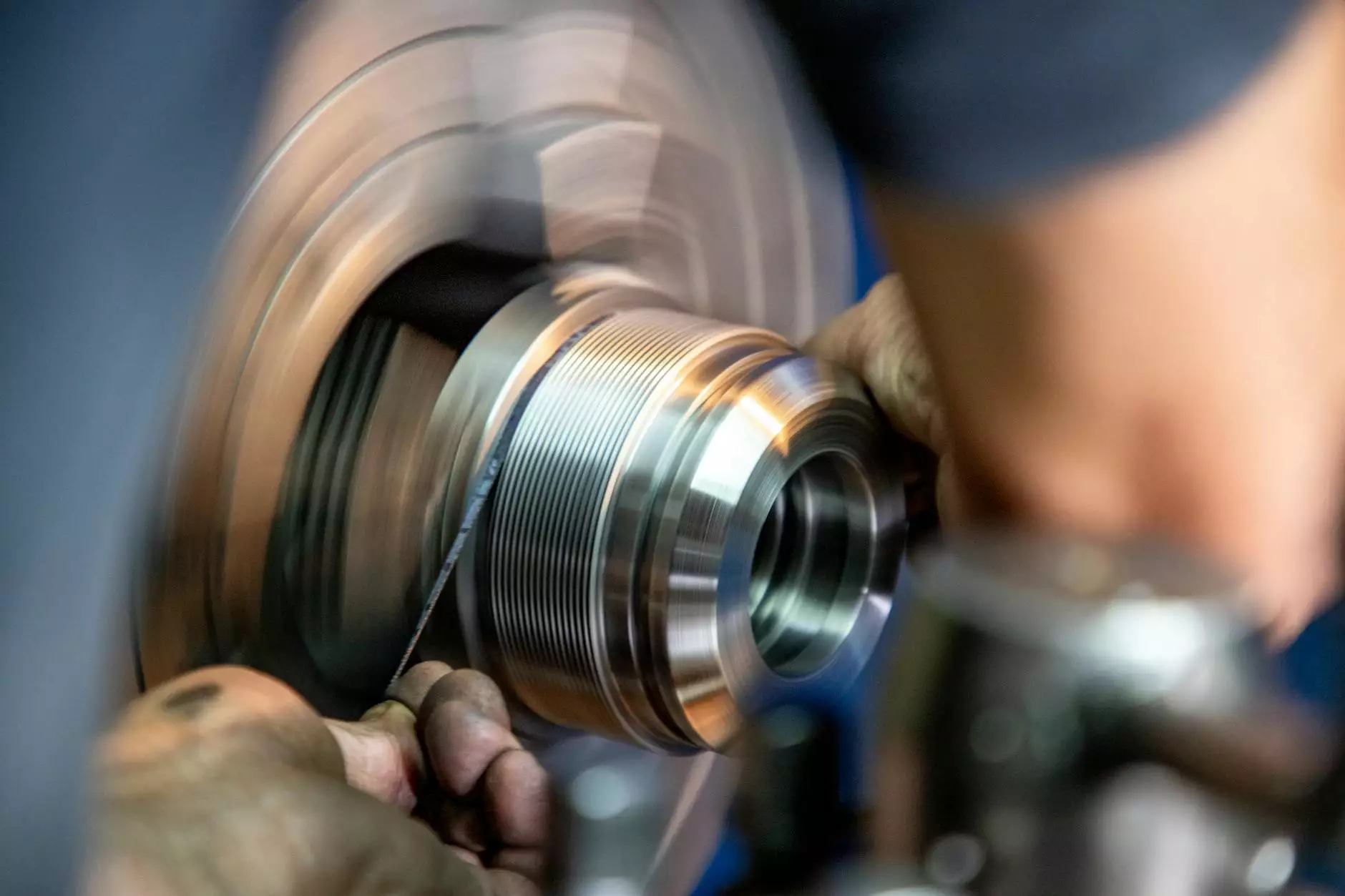
Custom CNC machining has revolutionized the manufacturing industry, providing unparalleled precision and efficiency. This article delves into the various aspects of custom CNC machining, its applications, benefits, and why it is essential for businesses looking to enhance their production capabilities.
What is Custom CNC Machining?
At its core, custom CNC machining refers to a manufacturing process where pre-programmed computer software dictates the movement of factory tools and machinery. This technology allows for the automation of complex tasks, ensuring consistency and accuracy in production. Whether it's cutting, drilling, milling, or engraving, CNC machines can perform these functions with remarkable precision. The term "custom" signifies that these processes can be tailored to meet specific project requirements, making CNC machining a versatile tool in modern manufacturing.
Key Features of Custom CNC Machining
- Precision and Accuracy: CNC machines operate with high levels of precision, reducing the margin of error that may occur in traditional machining processes.
- Versatility: Custom CNC machining can be adapted to produce a wide variety of parts and components from different materials, such as metals, plastics, and composites.
- Automation: CNC machining reduces the need for manual intervention, allowing for faster production cycles and lower labor costs.
- Consistency: With CNC machining, businesses can expect uniformity in product quality, as machines can replicate processes exactly every time.
- Complex Designs: CNC machining can easily handle intricate designs and complex geometries that would be challenging to produce by hand.
Applications of Custom CNC Machining
The applications of custom CNC machining are vast and span multiple industries. Here are some prominent sectors where CNC machining plays a critical role:
1. Aerospace Industry
In the aerospace sector, precision is vital. Custom CNC machining is used to produce components such as brackets, housings, and landing gear parts. These components must adhere to strict safety and performance standards, making CNC technology indispensable.
2. Automotive Manufacturing
The automotive industry relies on CNC machining for the production of engine blocks, transmission housings, and other essential components. The ability to create intricate parts quickly and accurately allows manufacturers to enhance performance and meet regulatory requirements.
3. Medical Devices
Custom CNC machining is crucial in the medical field, where precision is paramount. Manufacturers utilize CNC technology to create surgical instruments, prosthetics, and implantable devices that require exact specifications to ensure patient safety and effectiveness.
4. Electronics and Telecommunications
With the rapid development of electronic devices, there is a growing need for precision parts. Custom CNC machining produces casings, housings, and connectors that are integral to the functionality of electronic products.
5. Industrial Equipment
Many industrial machines are composed of parts produced through CNC machining. Gearboxes, pumps, and custom tooling are just a few examples where manufacturing precision can lead to improved operational efficiency.
Benefits of Custom CNC Machining for Businesses
Investing in custom CNC machining provides businesses with numerous advantages that enhance productivity and profitability. Here are key benefits to consider:
1. Cost Effectiveness
Although initial setup and CNC machine investment can be high, the long-term savings are considerable. CNC machining minimizes waste and reduces production costs due to its efficiency and speed.
2. Quick Turnaround Time
CNC machining can significantly shorten production times. With automated processes, first runs are typically produced faster, allowing businesses to respond to market demands swiftly.
3. Improved Quality Control
Consistency is crucial in manufacturing. CNC machines provide precise control and monitoring capabilities, enabling more stringent quality assurance processes compared to manual machining.
4. Enhanced Competitiveness
By utilizing CNC machining, businesses can produce high-quality components faster than their competitors. This advantage can lead to increased market share and customer satisfaction.
5. Customization Benefits
Businesses can offer personalized solutions to clients through custom CNC machining. Tailored parts meet specific client requirements, leading to stronger customer relationships and repeat business.
The Custom CNC Machining Process
The custom CNC machining process typically follows several key stages, ensuring efficiency and high-quality output. Below is an overview of the most critical steps involved:
1. Design and Prototyping
The first step in the process involves creating a detailed design using CAD (Computer-Aided Design) software. Designers create a digital model that specifies dimensions, tolerances, and material types. Prototyping might be necessary to test the design's feasibility and functionality.
2. Programming
Once the design is finalized, engineers convert it into machine language through CAM (Computer-Aided Manufacturing) software. This step involves creating a program that instructs the CNC machine on how to execute the necessary operations to create the part.
3. Material Selection
Choosing the right material is critical for ensuring that the final product meets performance and durability specifications. Common materials include aluminum, steel, brass, and various plastics.
4. Machine Setup
During this stage, the CNC machine is prepared, and tools are selected based on the job requirements. Tool calibration ensures that the machine operates correctly throughout the machining process.
5. Machining and Finishing
With everything set up, machining begins. The CNC machine executes the programmed instructions to produce the part. After machining, additional finishing processes may be required, such as painting, anodizing, or polishing, to meet the desired aesthetic and functional requirements.
6. Quality Assurance
Before the final product is shipped, it undergoes rigorous quality inspection. This stage involves measuring tolerances, inspecting surface finishes, and ensuring that the finished component meets all specifications.
Choosing the Right CNC Machining Partner
When selecting a partner for custom CNC machining, businesses should consider several factors:
1. Experience and Expertise
Look for a company with a proven track record in CNC machining services. Experienced partners can navigate challenges and provide insights that less experienced manufacturers may overlook.
2. Technology and Equipment
Ensure that the machining partner utilizes modern, high-precision CNC equipment and software. Advanced technology can enhance production capabilities and increase efficiency.
3. Customer Service and Support
Effective communication and customer support are crucial. A responsive partner will work with your team throughout the design and production process, addressing any concerns that arise swiftly.
4. Quality Standards and Certifications
Verify that the CNC machining partner adheres to industry standards and possesses relevant certifications. Compliance with quality management systems like ISO 9001 is a strong indicator of reliability.
5. Flexibility and Scalability
A good partner should be able to accommodate changes in project scope or volume. Flexibility is essential, especially when adjusting to market demands or customer requests.
The Future of Custom CNC Machining
As technology continues to evolve, the landscape of custom CNC machining is anticipated to change significantly. Innovations such as artificial intelligence, machine learning, and additive manufacturing (3D printing) could enhance the capabilities of CNC machining, allowing for even greater precision and efficiency.
Additionally, the integration of the Internet of Things (IoT) could enable smarter manufacturing practices, where machines actively communicate and optimize their performance in real-time. Sustainable practices are also on the rise, with a focus on reducing waste and energy consumption in the manufacturing process.
Conclusion
In summary, custom CNC machining is a vital component of modern manufacturing, offering unmatched precision, efficiency, and versatility. By leveraging this technology, businesses across various industries can achieve higher productivity, better quality control, and enhanced competitiveness. Understanding the custom CNC machining process, its benefits, and how to choose the right manufacturing partner will empower businesses to take full advantage of this innovative technology.
For businesses looking to invest in custom CNC machining, exploring reliable partners like DeepMould.net can lead to fruitful collaborations that drive growth and success in today’s competitive market.